Process Mapping is a core tool in Lean Six Sigma and has many benefits other than the process map itself. NWCPE uses it frequently when working with customers as part of the journey to create consistent understanding of their processes within the employee base.
The essence of Lean Six Sigma lies in improving processes to improve output. After all, effective processes drive quality and customer satisfaction. However, these processes live in the abstract and can be exceedingly difficult to visualize before they are put into effect. The individuals involved in developing, measuring, and analyzing the processes likely have different visions themselves about how that process should perform.
So, how do you bring all the key players together and develop a clear understanding of the process? With a process map, of course. These workflows serve as reference points for any project team.
Truth be told, process mapping can be tedious, time-consuming, and frustrating. Still, the actual creation of the process map is more important than the tangible document as the development brings about a clear understanding of how the process behaves and how it can be improved. Shortcuts may be tempting but resist the urge to take the easy way out. Instead, reap the fruits of process mapping development by following best practices. The following are a few of the best practices recommended.
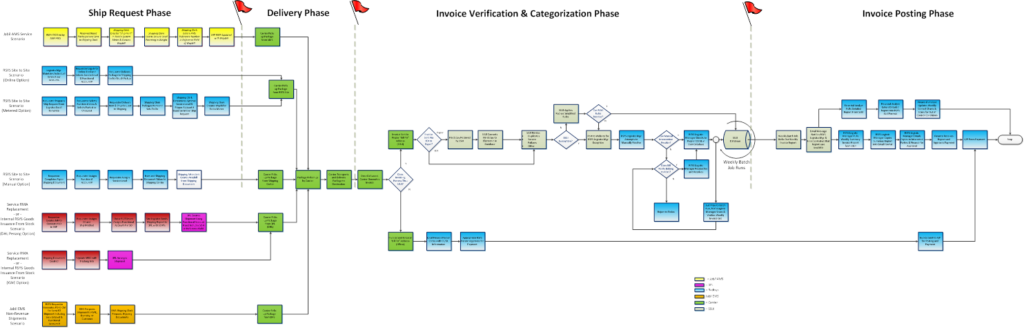
Guidelines for Successful Lean Six Sigma Process Mapping
Process Mapping with the Key Players
Bring all the key players into the process map development from the beginning. Each party should be included in the map creation process simultaneously for maximum benefits. First, you’ll receive clarity on each person’s individual visualization of the process, which helps to create a cohesive reference point that includes everyone’s understanding. Each key player will bring different areas of expertise to the table and can document the areas of the process they know best. Next, as everyone gets to know the process better, they’ll also develop a greater understanding of how their role fits into the process.
As the conversation moves to discussing the future state of the process, each key player will be able to suggest ideas for improvement from their understanding of the process in general and from the vantage point of their role in the process itself. Finally, because you’ve chosen to involve everyone in the process, you’ll get more buy-in when you start to implement those changes.
Have a Beginning and an End
No map goes on forever; a beginning and end point are essential to ensuring that the journey brings you to the right destination. Always develop your processes with a beginning and end in mind. By that same token, it’s beneficial to set boundaries regarding how much detail your process map will include. If this is your first time process mapping with your team, you may find it more fruitful to begin with an overview and then dive deeper into the details as your team’s understanding improves. Regardless, always map out the steps of the process so its sequence is understood by all.
Put the Process Map into Action
Even the best process map can be rendered ineffective if it is never applied and tested. The point of process mapping is not to create another document that merely collects dust. Instead, make your process map come to life by putting it into effect. Get out there and walk the process by taking it from your computer to where the action is.
As you analyze the process map’s performance, be sure to make note of how tasks are being performed. If they don’t match up with what’s on your process map, find out why. Is it a lack of understanding or is there something about the process that doesn’t translate to “real life?”
Have someone from outside your project team work the process from end to end using your map. Document which aspects are successful and which are not. You may find you need more detail to make the process map work.